Multi-connector USB-C charging cables, which allow you to charge multiple devices simultaneously using a single USB-A port, are certainly convenient. These cables typically feature one data-capable connector and multiple charging-only connectors, making them seemingly ideal for powering multiple devices on the go. However, as with many technological conveniences, there are hidden risks.
Recently, I purchased a 1-to-4 USB-A to USB-C charging cable. This cable includes one data cable and three charging cables. Initially, it seemed like a great way to simplify my charging setup. However, I soon discovered a significant design flaw: the voltage on the V+ line follows the voltage requested by the device on the data cable.
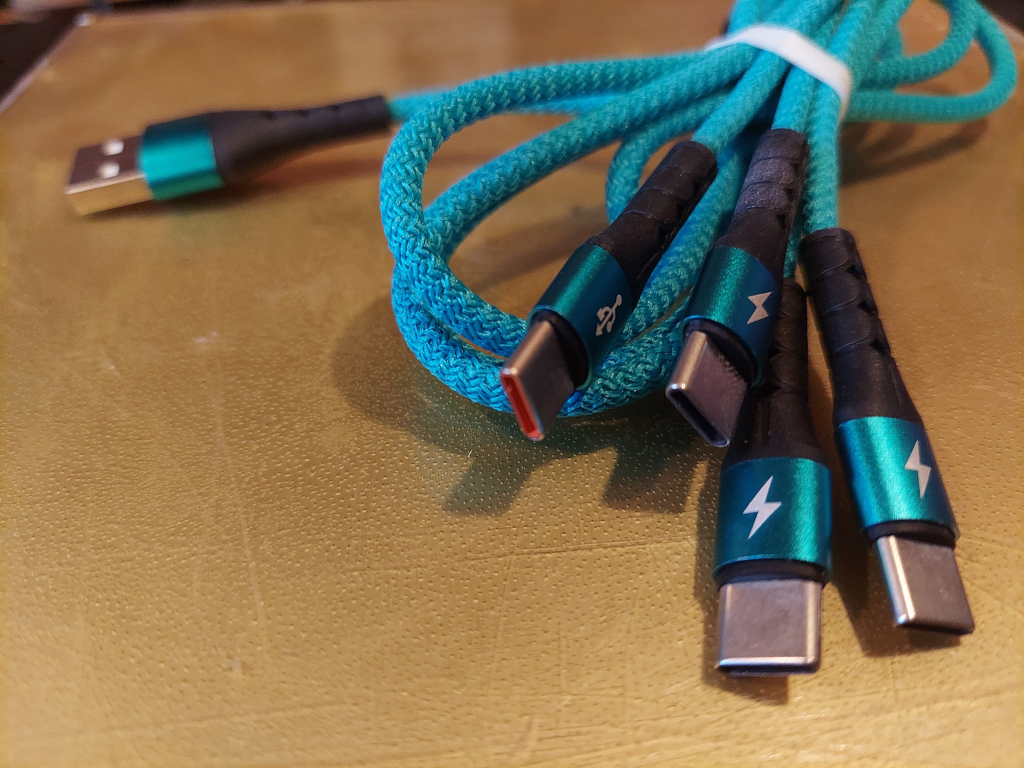
USB defaults to +5VDC power, which has been the standard since USB first came out. (How much current a device should draw is another discussion.) But with the USB-C Power Delivery (PD) specification, USB-C capable devices can request higher voltages and/or current limits, which will then cause the power supply to change to that higher voltage.
For example, when I connected my Samsung A71 phone to a power bank via this cable’s data connector, it requested and received 9V on the power rail (as measured by a handy passthrough USB analyzer.) This 9V was then applied across the V+ lines on the other three cables, potentially subjecting any devices connected to the charging-only connectors to a voltage they were not designed to handle. (Needless to say, I suspect this cable is not standards-compliant. Hey, it was cheap.)
USB-C Power Delivery (PD) is a specification that allows devices to negotiate the power they receive. This negotiation can result in voltages of 5V, 9V, 15V, or even 20V, depending on the device’s requirements and the charger’s capabilities. While PD provides a great way to supply more power when needed, it also introduces risks when multiple devices are connected without proper isolation.
Not all USB-C devices are tolerant of higher voltages. Many devices that do not support PD negotiation are only rated for 5V. If these devices are exposed to higher voltages, they can be damaged or even rendered inoperable. This makes it crucial to ensure that devices on the charging-only connectors are either capable of handling the higher voltage or are protected from it.
If you’re charging four of the same type of thing (like those USB-rechargeable AA batteries), such cables will probably generally work (as long as the individual devices don’t draw too much power without negotiating for it.) But if you just plug in devices to charge them (as many purchasers of these cables will no doubt do), take care that the data-cable device doesn’t see a native USB-C connection, request 20V to fast-charge itself, and fry the rest of the devices connected to the cable.
After all, power is proportional to V2, so a device drawing 1x power at 5V will draw 16x the power at 20V, assuming it is essentially a resistive load. This will usually end with some part of the device releasing its magic smoke due to trying to dissipate 16x as much power as it should.
So, while there are good uses for such cables — use them carefully!
Coauthored with GPT-4o.
(They wrote the article from a description I provided; I edited for style.)